Understanding the Role of Rotomolding in Custom Plastic Production
Understanding the Role of Rotomolding in Custom Plastic Production
Blog Article
Rotational molding, or Rotomolding, has turned into a chosen manufacturing process for creating resilient and supreme quality plastic parts. Their special process, which requires heating and twisting products inside a mold, assures evenly spread power and reliability in the final product. This blog considers the extraordinary advantages of Rotational Molding and why it's gained prominence as a strategy for providing hard and long-lasting plastic components.
Remarkable Strength with Standard Wall Width
One of the essential strengths of rotomolding lies in its power to make areas with uniform wall thickness. Unlike different production methods that will keep irregular or slim places susceptible to weakness, rotomolding guarantees consistency in most layer. By equally heat and rotating the mold, the molten resin passes efficiently, making seamless and powerful plastic pieces that will tolerate major masses and withstand impact.
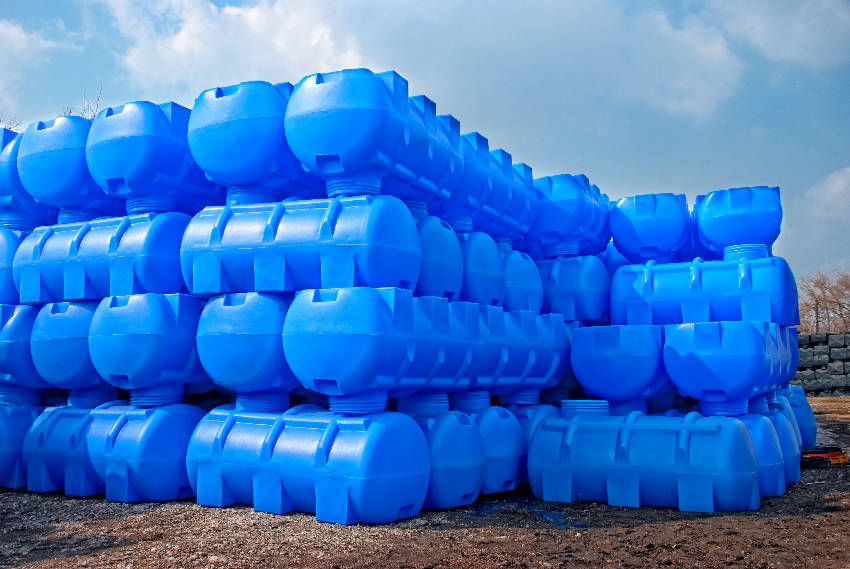
This function makes rotomolded components ideal for purposes requesting architectural integrity, such as for example big tanks, playground gear, and professional containers.
Improved Toughness with Stress-Free Molding
Stress can destroy plastic parts, impacting their lifetime and performance. Fortuitously, the rotomolding process eliminates central stresses usually present in other molding techniques. Because no high-pressure allows are employed during production, the plastic material experiences minimal stress, resulting in a stronger product that works easily over time.
Moreover, the lack of seams or weld lines increases the general toughness of rotomolded elements, making them resilient to cracking, splitting, and environmental wear and tear.
Outstanding Flexibility and Modification
Rotomolding presents unparalleled style flexibility, enabling suppliers to generate complicated designs and structures with precision. The ability to incorporate included functions like bones, positions, or consistency assures that the last item matches specific practical or cosmetic requirements.
This method also helps the utilization of a wide selection of components and chemicals, such as UV stabilizers and colorants, more improving durability by creating pieces tolerant to facets like sunlight coverage, diminishing, and substance damage.
Resilience in Intense Situations
Rotomolded parts are developed to last, even when subjected to extreme environments. They maintain their strength in hard conditions, fight corrosion from substances, and experience prolonged outside use. This makes them particularly valuable in industries like agriculture, construction, and marine programs, where components experience difficult problems daily.
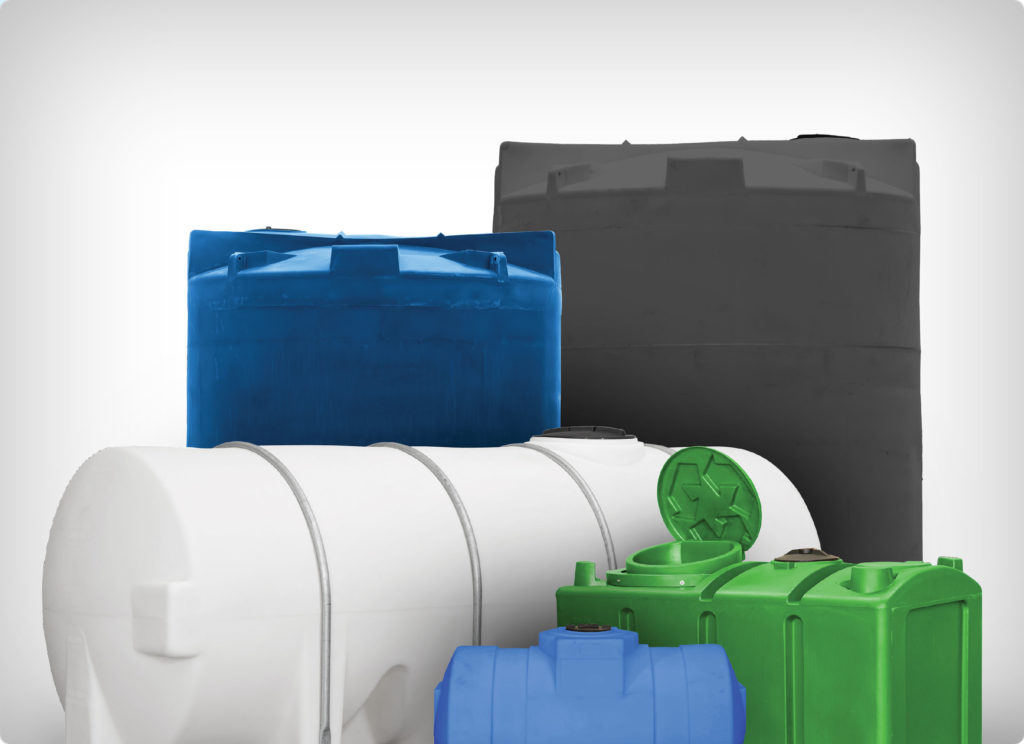
Their capacity to execute dependably in such settings reduces the requirement for frequent alternatives, making rotomolded pieces both cost-effective and sustainable.
Driving the Future of Durable Plastics
The increasing demand for reliable and sturdy plastic parts continues to position rotomolding at the lead of manufacturing innovation. Using its detail, stress-reducing benefits, and ability to resist varied surroundings, rotomolding is surrounding the way in which industries prioritize energy and endurance inside their products. By buying that sophisticated method, makers may make plastic parts that stand the test of time.
Report this page